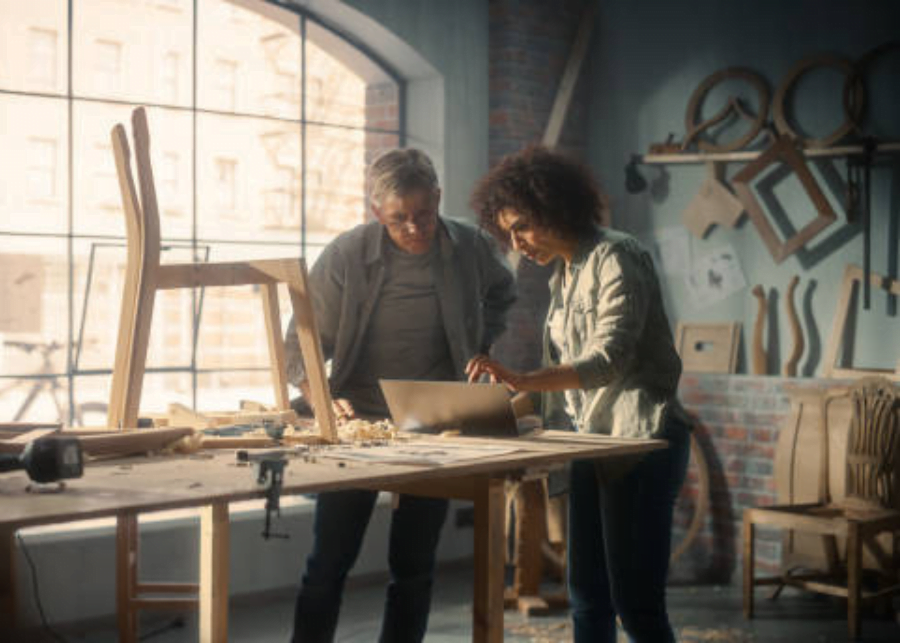
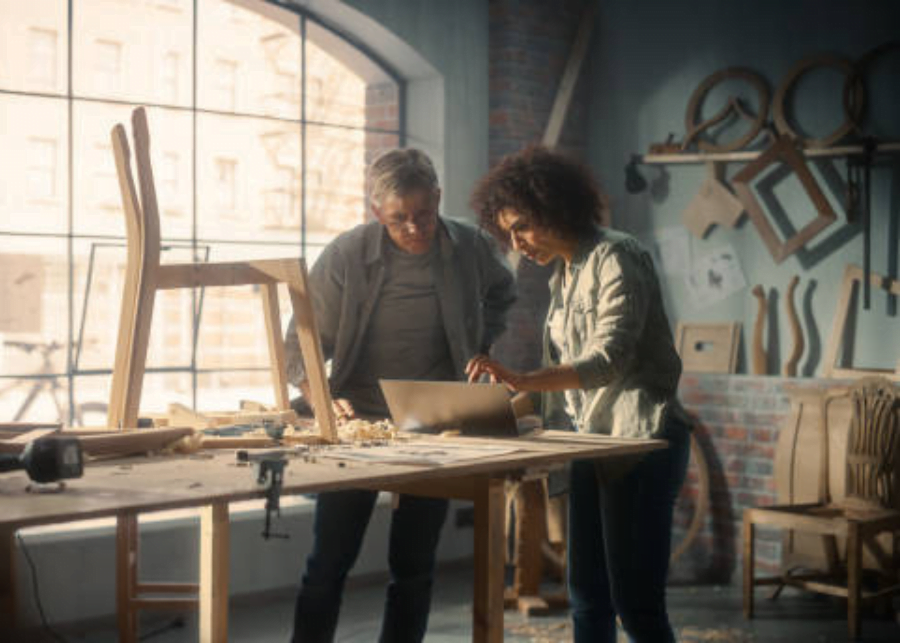
Table of Contents
I’ll tell you my process for making detailed full-color woodworking plans that I sell. I’ll let you in on some secrets and tell you how much money you can actually make doing that.
We basically focus on a concept called “shock greatness. Which means that I tend to build and highlight projects that make your shop or workshop better and more efficient. Part of that is making woodworking plans so that you can do it yourself. Now, making woodworking plans and selling them is not exactly a novel concept if you watch other making channels like mine; almost all of us do it. Why would you want to listen to me about making woodworking plans?
It sounds pretty simple. Well, to establish credibility and not to brag or gloat, I promise I have literally made tens of thousands of dollars selling woodworking plans on Etsy. And I don’t have hundreds of plans available. I have, I think, 11 or 12. I think there’s some value I can share with others on how to make woodworking plans or maybe how to improve your current woodworking plans so that you can sell them.
Now, even if you’re not going to go sell woodworking plans, I think there’s value in how I’ve figured out how to do this. Hopefully there’s something that you can take away. Now, here to keep it simple, I’m going to make a single drawer box from beginning all the way through to the build plans. Obviously, this is a short example, but the concepts are all the same. Alright, Let’s get down to business.
How do I make woodworking plans?
Well, as I’m planning any project, I always start with a pencil and a sheet of paper. For me, there’s just something about sketching with a pencil that kind of lets me wrap my head around exactly what I want to do. I kind of work outside in, so I look at the major dimensions. Maybe this thing has to fit within a space or, in the case of a drawer, it has to fit within an opening in a cabinet.
And then I work backwards from there. Okay, so I think about the joinery, I think about the materials, and from there, I usually have a pretty clear idea of how exactly I want to do this. Once I have that sketch, I then sit down at the computer and actually start 3D modeling. Now, this is the step that scares a lot of people. Whoa, 3D modeling. I mean, I get it, it’s intimidating. Two of the most common platforms for woodworking are SketchUp and Fusion 360.
SketchUp is okay, but if you had to start from scratch, I would urge you to go towards Fusion 360. And there are a couple of reasons why. Number one, it’s a heck of a lot more powerful. You can get away with doing very simple things on SketchUp, and for most people, that might be okay. But if you ever want to progress past simple woodworking projects or you want to divert into other technologies, Fusion is that direct insertion point. SketchUp kind of hits a brick wall.
And number two, Fusion 360 is backed by Autodesk, a major CAD software company, and they’re constantly putting out updates and improving the software. SketchUp, I really don’t know, to be honest, their background, but it’s not Autodesk. The natural first question I get is, “Okay, I’d love to use Fusion 360. How do I get started?” I always point people towards the Fusion 360 course by Kevin Kennedy.
Now, this is a paid course, it’s not free, but I’m telling you, you are getting your money’s worth. I’ve done 3D modeling for the past 10 years or so because of my career, so learning Fusion 360 was a much smaller learning curve for me. But learning from scratch, there are a lot of mistakes and bad habits that you can get into, which is going to cause a lot of heartache down the road.
By taking a course like Kevin’s, you’re going to start off on the right foot, you’re going to be efficient, you’re going to be quick, and you’re going to be much happier in the long run. If you’re curious, just go check it out. There’s a link in the video description below. Kevin’s a great teacher and you won’t be disappointed. Now, there’s a fundamental benefit to modeling in 3D for a woodworking project, and that is that you get to make all of your mistakes digitally.
I know I’m no different than any of you, but we’ve tried to wing projects before, and mistakes happen, and your project just ends up being kind of so-so. If you start instead with a 3D model and you get to build the whole project through and understand what you need to think about and think ahead for, it always seems to turn out a lot better.
And then, if you are going to make build plans, at least in my case, it is an absolute requirement, because I use the 3D model to create the illustrations that go into the build plan. For the drawer example, it consists of two sides, a front, a back, and a bottom. But we’re going to start by drawing the sides. Now, in this case, I’m making them out of 1 by 8 pine, and then I’m actually going to cut a rabbet at each end for the joinery.
Now, my sketch actually comes in handy here in understanding how these things need to fit together to get my final drawer dimension. But again, because you’re doing it digitally, you could fit it up one way and realize that you got your dimensions wrong, go back and tweak something, and then get it right. Once I’ve verified that my box is the right size, I can now add the bottom panel. Here you see a complete drawer.
This is where your 3D model comes in very handy, and specifically Fusion 360. I can actually orient my parts in a certain way that I want to show the customer, and then export that image with a transparent background, and then place them directly into my PowerPoint plans.
Now that we’ve got our drawer modeled, we can now move into making the plans themselves, because remember, we’ve made all our mistakes digitally. Now we can move on to the real world. Quick break to talk about the sponsor of today’s video, and that is tedsplansdiy. Tedsplansdiy is an online community for creative people with thousands of classes ranging from advertising to illustrations to photography.
Well, tedsplansdiy has a ton of classes. There’s some on the basics of Etsy, how to set up a successful store, how to optimize shipping, how to run ad campaigns. You get the picture. Now, what’s cool about Tedsplansdiy is although there is a tiny cost associated with a membership, there are no ads. So you don’t have to sit through one of these in one of those classes, and you can have multiple classes going on.
I’ve been a huge fan of LEGO ever since I was a kid, and for me, the gold standard for instructions is a LEGO instruction manual. They take something that’s pretty complex if you think about it and reduce it to a series of full-color pictures and symbols. I love the fact that there are no words; they can convey a very complicated task without having to explicitly tell me how to do it. This has been something that I’m trying to achieve. I am nowhere near there right now, but it’s where I want to get to.
To lay out my build plans, this is gonna sound weird, but I use PowerPoint. Yeah, you heard that right. Now, I will probably move away from PowerPoint in the near future into something a little bit more professional, but for now, PowerPoint actually works really well.
I’ve actually created a template on which I make all of my build plans, but the template basically just consists of some branding, maybe a version number, and finally, a page number. Everything else, of course, will be specific to the project.
The basic components of a successful woodworking plan
Now, the basic components of a successful woodworking plan, in my opinion, start with an initial disclaimer. Now, every one of my plans has one of these, and all it basically is saying is, “This is what you’re building. Here’s how big it is. If you want to make any changes, do that now.” Because the last thing you want is somebody to get through this project and realize, “Oh, it’s too big for my space.”
And I know that sounds dumb, but I think there’s value in doing that. In the case of my ultimate cabinet build, there are several configuration. I talk about that in the beginning. If you have limited space you need to work with and you need a smaller version of that, that’s where you get that information. You get what you need.
The first real section is a master material list. This includes everything that they will need to complete this project, including raw material like wood parts and even fasteners. What this does for you as a content creator is the opportunity to add affiliate links and make sure that they have exactly what they need and they don’t have to go digging for it.
The master material list is a master cut list
Following the master material list is a master cut list. Now, this is very important, especially for big projects, because you want to help them optimize their materials so they don’t have a bunch of waste at the end of this. It also helps them wrap their mind around how much this is going to cost and potentially how long it’s going to take.
Now, to build the cut sheets, I used to make them by hand, but I actually found a really great free resource called Cut List Optimizer. After the master material list and the master cut list, you can start into the meat of the plans. Now, for this example, we’re building one drawer box, so that’s the entirety of the plan.
But if you’re building, say, a cabinet with many drawers, you might first choose to build the cabinet and then move on to building the drawers. The first section would be just the cabinet carcass itself. It would have its own sub-material list and sub-cut sheet. I think there’s a ton of value in creating bite-sized chunks that people can tackle, especially on big projects.
In the plans themselves, I always start with secondary operations on the stock material, and on top of just describing what needs to be done, I like to include a couple of options on how they might do it. Because again, I don’t want to assume that everyone’s an expert. Here, I’ll say, although I used a palm router, you could also use a router table or a dado blade in your table saw.
And oh, by the way, for this particular case, if they’re setting up that router with that rabbeting bit and getting it dialed in, if there are any other rabbits in this project that require those dimensions, I like to mention it here. If you were building this, you would like to know that because you don’t want to go set this back up again. I like to include any warnings if possible.
In this case, there’s actually a couple of ways you can assemble the drawer box and end up with the wrong dimension drawer. Specifically, call that out and make it very obvious. I like to err on the side of caution in this case. You want them to have a good time building this; you don’t want them to get to the end and realize all their drawers are the wrong size.
Once the main instructions are done, I always like to follow it up with an index with some resources. Now, in my case, I usually do a build video to go along with the plan, I’ll link those videos directly. But this is also a good place to include things like tables or reference diagrams or maybe even some examples of tools that you found very useful during the build. From that PowerPoint file, we then create a PDF. The PDF just makes it universal so anybody can print it out.
Alright, so some last-minute takeaways to making successful woodworking plans that you can sell: visual is key, and in my opinion, I think color is better. Make sure you include upfront parts lists and cut sheets, as well as sub-parts lists and sub-cut sheets. Keep going back to thinking about how you would build it and what you would like to have if you were in their position.
Break the project up into logical steps; try and use text sparingly. I have not mastered this yet. I wish I was better at this, but I want to get to the point where mine have very little, if any, text. And that leads directly into the next one, and that’s keep it concise. Although I tend to err on the side of detail, there is a sweet spot, and nobody wants to download a thousand pages on how to make a bookcase.
There you have it. You have a build plan that you can distribute out to customers, you can charge people for, you can give it away for free, whatever you choose to do. And this is where the topic of your platform comes into play. I have sold all of my build plans on Etsy, and a lot of people ask me, “Why would you do that?” Most content creators and woodworkers sell them directly on their website, and there are absolutely pros to doing that.
I would argue that there are more pros by using a platform like Etsy. The biggest one is that you have a much bigger audience. I can attribute a significant amount of my sales coming from sources other than my YouTube channel. You just wouldn’t have that traffic on your little website. Now, the downsides of using a platform like Etsy is, of course, they take a fee of every single sale that you make. It ends up being a very small
Process for making detailed full-color woodworking plans
Process for making detailed full-color woodworking plans that. I’ll let you in on some secrets and show you how much money you can actually make doing that. As I’m planning any project, I always start with a pencil and a sheet of paper. For me, there’s just something about sketching with a pencil that kind of lets me wrap my head around exactly what I want to do. I kind of work outside-in, so I look at the major dimensions, maybe this thing has to fit within a space, or in the case of a drawer, it has to fit within an opening in a cabinet.
And then I work backward from there. Okay, so I think about the joinery, I think about the materials, and from there, I usually have a pretty clear idea of how exactly I want to do this. Once I have that sketch, I then sit down at the computer and actually start 3D modeling.
Now, this is the step that scares a lot of people. Whoa, 3D modeling? I mean, I get it, it’s intimidating. Two of the most common platforms for woodworking are SketchUp and Fusion 360. SketchUp is okay, but if you had to start from scratch, I would urge you to go towards Fusion 360. And there are a couple of reasons why. Number one, it’s a heck of a lot more powerful, so you can get away with doing very simple things on SketchUp, and for most people, that might be okay.
But if you ever want to progress past simple woodworking projects or you want to dive into other technologies, Fusion is that direct insertion point. SketchUp kind of hits a brick wall. And number two is, Fusion 360 is backed by Autodesk, a major CAD software company, and they’re constantly putting out updates and improving the software. SketchUp, I really don’t know, to be honest, their background, but it’s not Autodesk.
The natural first question I get is, okay, I’d love to use Fusion 360. How do I get started? I always point people towards the Fusion 360 course by Kevin Kennedy. Now, this is a paid course, it’s not free, but I’m telling you, you are getting your money’s worth. I’ve done 3D modeling for the past 10 years or so because of my career, so learning Fusion 360 was a much smaller learning curve for me.
But learning from scratch, there are a lot of mistakes and bad habits that you can get into, which is going to cause a lot of heartache down the road. By taking a course like Kevin’s, you’re going to start off on the right foot, you’re going to be efficient, you’re going to be quick, and you’re going to be much happier in the long run. If you’re curious, just go check it out.
Now, there’s a fundamental benefit to modeling in 3D for a woodworking project, and that is that you get to make all of your mistakes digitally. I know I’m no different than any of you, but we’ve tried to wing projects before, and mistakes happen, and your project just ends up being kind of so-so.
If you start instead with a 3D model, and you get to build the whole project through and understand what you need to think about and think ahead for, it always seems to turn out a lot better. And then, if you are going to make build plans, at least in my case, it is an absolute requirement because I use the 3D model to create the illustrations that go into the build plans.
For the drawer example, it consists of two sides, a front, a back, and a bottom. But we’re going to start by drawing the sides. Now, in this case, I’m making them out of 1 by 8 pine, and then I’m actually going to cut a rabbet at each end for the joinery.
Now, my sketch actually comes in handy here in understanding how these things need to fit together to get my final drawer dimension. But again, because you’re doing it digitally, you could fit it up one way and realize that you got your dimensions wrong, go back and tweak something, and then get it right.
Once I’ve verified that my box is the right size, I can now add the bottom panel. Here you see a complete drawer. This is where your 3D model comes in very handy, and specifically Fusion 360. I can actually orient my parts in a certain way that I want to show the customer and then export that image with a transparent background and then place them directly into my PowerPoint plans.